Gaskets for Engine
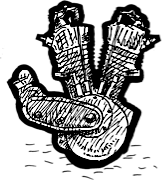
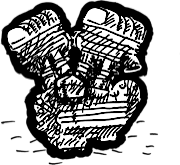
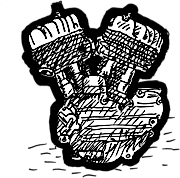
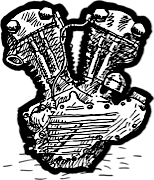
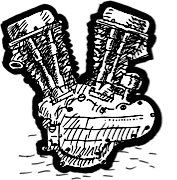
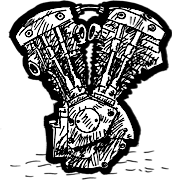
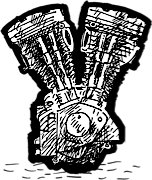
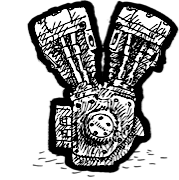
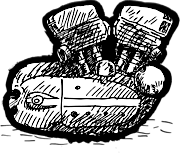
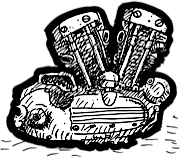
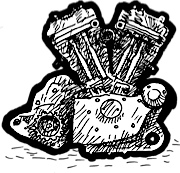
Engine gaskets
The first singles and twins from Harley-Davidson were hardly dependent on gaskets. There was a flat gasket under the cylinder base flanges and then another under the drive case cover and one under the later oil pumps. Brass sealing rings were installed in the intake flanges and housings - practically endlessly reusable if treated well. Bearings and bushings were designed by the engineers and manufactured by the workers to fit in such a way that seals were not necessary or intended at all. The output shaft ("sprocket shaft") had a felt ring as a carrier for the sealing grease packing. You can actually seal an engine with such simple means - i.e. as tightly as was necessary for perfect engine running at the time.
Engine sealing kits: available from side valve engines in 1926
Even as a single cylinder, the side-valve engine has more gaskets than a F-head twin from the early 1920s. It is therefore always worth using a complete gasket set when overhauling an engine. All gaskets in the required quality in one bag: this is the carefree package for the engine rebuilder. Available for all air-cooled 4-stroke Harley engines from the side valve series (A and B (without AA and BA), V, U, W). For models from 1937 onwards including primary gasket.
Head gaskets, the crux of the Harley engine
The side-valves, i.e. A and B models with 350 cc from 1926 and their successors including the 750cc two-cylinders and then of course the big twins with 1200 and 1300 cc, were the first Harleys with cylinder head gaskets. In terms of casting technology, the slightly labyrithine combustion chamber is easier to implement with a multi-part design. And when decoking valve heads and piston crowns, it is simply practical to be able to remove the cover on the cylinder.
On all OHV engines from Harley-Davidson - i.e. those with the valves in the cylinder head: Knucklehead, Panhead, Sportster, Shovel through to the Milwaukee Eight - it is not possible to install the valves without a joint between the head and the cylinder.
The cylinder head gasket, which takes care of this joint between the cylinder and the head, has a tough job. In addition to pressure, it also has to withstand heat. This is why metal-reinforced material is often used at this point. The mechanic can make the gasket's job easier by adhering to torque values - where specified by Harley in the manual - and - where there are no specifications - by at least making sure that the cylinder head bolts are tightened crosswise and evenly.
Cylinder base gasket: important for engine breather functionality
The gasket between the crankcase and the cylinder is the cylinder base gasket. Without this seal, the engine would leak due to the internal pressure of the crankcase. In the Harley-Davidson V2, the two connecting rods run on the same crankpin. On each downward stroke, the pistons compress the air beneath them, i.e. in the crankcase. On the upstroke, they then generate a vacuum. The positive pressure escapes via the rotary valve ("breather valve") in the right-hand half of the crankcase and the engine ventilation, while the negative pressure supports the oil supply to the cylinders and pistons. This is a finely tuned system. If the cylinder base gasket leaks, this functionality is void.
How can the mechanic support the cylinder base gasket?
On all engines from Evolution upwards, the correct torque and tightening pattern of the cylinder head nuts is important, because the cylinder is held - together with the cylinder head - by long stud bolts. The stud bolts are special tension bolts. If the cylinder head and cylinder base gaskets are constantly leaking for no apparent reason, the stud bolts should be replaced.
On older engines, the cylinder is held to the crankcase by four short stud bolts. To avoid distorting the cast-iron flange when tightening the nuts, tighten them crosswise, first a little more than hand-tight, then end-tight. However, end-tight does not mean that you bolt down the nuts like mad. It is better to warm up the engine carefully and retighten then the nuts on the hot cylinder flange - again crosswise.
With cast iron cylinders, the flange can warp. This is because the cylinders are only held at four points and the contact pressure mainly acts on these four points instead of on the entire sealing surface as with the Evo. This is why you should always check the flange to make sure it is straight before fitting the cylinders to the piston.
Don't use just any gasket, but quality products from James, Cometic or S&S. Particularly in the case of big bore cylinders with really narrow sealing surfaces, carefulness and good work are required during installation.
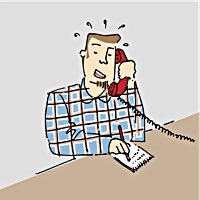
Have any questions?
Our service team will be glad to help out: Mondays - Thursdays 08:00-17:00 CET, Fridays 08:00-16:00 CET, Phone: +49 / 931 250 61 16, eMail: service@wwag.com