Threads: Make and Repair
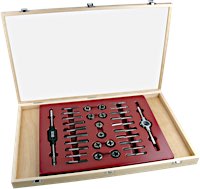
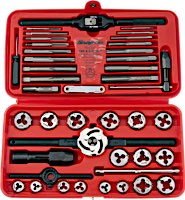
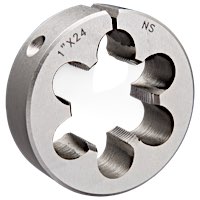
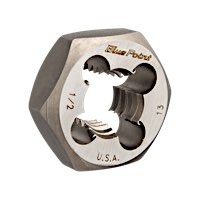
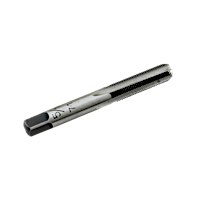
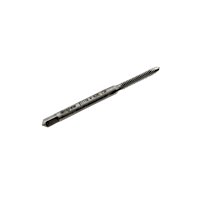
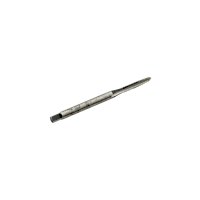
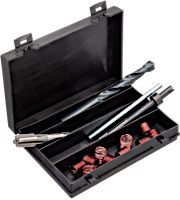
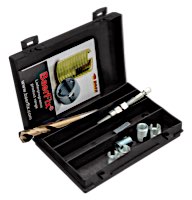
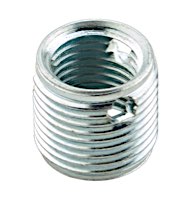
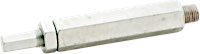
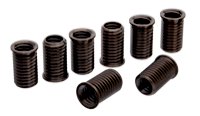
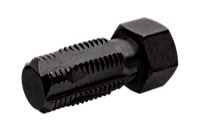
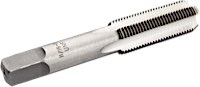
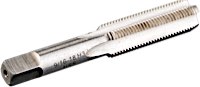
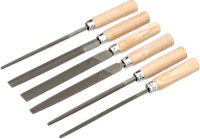
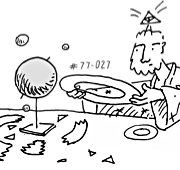
Cutting threads, repairing threads
Nails or rivets can only transmit tensile forces along their axis. A screw thread divides the tensile forces between the individual turns of a helix and thus multiplies the force transmission. Threads and threadlike things are a really old story ... However, screws with standardized threads as fastening and adjusting elements are an invention of the 19th century. Increasing mechanization and mass production pushed for uniform and interchangeable screws and nuts. A certain Mr. Whitworth was the first to specify the inner and outer diameters, pitch and flank angle in tables for his products. Because Harley-Davidsons are an originary American motorcycle, all air-cooled Harleys to this day have bolts and nuts installed or threads cut into the housings that comply with the standards of the Society of Automotive Engineers (SAE).
Tools for threads that are measured in inches - where can I find them?
The tools for such threads are available here at W&W Cycles:
- Complete sets of taps and dies for external and internal threads
- Individual taps for internal threads and dies for external threads
- Repair kits for stripped spark plug threads
- Repair kits for the Harley-specific but otherwise super-rare 1/4"-24 threads or for the 7/16"-16 threads of cylinder head bolts that neither conform to any standard
- Repair taps for timing holes and drain threads
Cut vs. formed threads
The tools in our range can be used to cut threads, i.e. remove them with chips. The threads of standardized screws are rolled like those of spokes, i.e. cold formed. This procedure displaces the material rather than removing it. It also compacts the surface at the same time. Standard threads in engine housings are also formed rather than cut in industrial production and are therefore more durable. Are threads produced with W&W Cyles threading tools therefore inferior to industrially formed threads? The answer is clear: not at all, as long as the threads are cut carefully and quality material is used. Simply select a steel grade that is stronger than usual industry-standard and ensure that the core holes are as narrow as possible when drilling internal threads. If you prefer extra pull-out strength, use a coil insert or a threaded bush. This is also possible with the tool kits from W&W Cycles.
Tapping threads - what do I look out for so that the result is clean and lasts a long time?
The diameter of the core hole must be right for internal threads. If you have tables at hand you will want to look it up there. If no tables are available to you, you can use a rule of thumb to determine the core hole:
- Outer Ø minus pitch equals core Ø. As on metric threads the pitch of American threads is the distance from thread tip to thread tip. It is very easy to calculate:
- 25.4 mm ÷ number of threads/inch = pitch.
For a 5/16"-24 thread, the pitch is therefore 25.4 mm ÷ 24 = 1.06 mm. According to our rule of thumb, the core hole is: 7.94 mm - 1.06 mm = 6.88 mm. Suitable drill bit sizes would therefore be 17/64" or 6.9 mm. If you simply use a 7 mm drill bit because you don't have a 6.9, you will find that the tap goes in easier and also is easier to turn, but you will remit a certain percentage of the thread strength. Oil helps against sticky taps. If you don't have cutting oil, use WD40 or PanAm Pan-a-Lube. External threads are cut with oil, too. Oil cools the tools' cutting edges and helps with removing the chips. The diameter of the round steel into which you cut should be just a trifle smaller than the nominal thread diameter. To ensure that the thread cutting die and tap grip well from the beginning, you will chamfer the round steel bar and countersink the core holes. This way, your DIY-cut thread will definitely be a a story of success.
Repairing threads
This task usually is about stripped internal threads in engine or gearbox housings or similar components. Basically, the old, destroyed threads are completely drilled out and the new hole is armored with an insert. For threads that are subject to high thermal stress, such as spark plug threads, a sleeve insert is recommended rather than a wire insert.
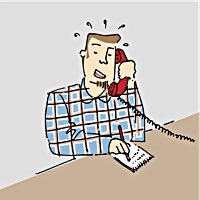
Have any questions?
Our service team will be glad to help out: Mondays - Thursdays 08:00-17:00 CET, Fridays 08:00-16:00 CET, Phone: +49 / 931 250 61 16, eMail: service@wwag.com